(2)
Interval Column. This column tells you
when you must do the procedure in the procedure
column. BEFORE procedures must be done before you
operate or use the equipment. DURING procedures
must be done during the time you are operating or using
the equipment for its intended mission. AFTER
procedures must be done immediately after you have
operated or used the equipment.
(3)
Location, Item to Check/Service Column.
This column provides the location and the item to be
checked or serviced. The item location is underlined.
(4)
Procedure Column. This column gives the
procedures you must do to check or service the item
listed in the Check/Service column to know if the
equipment is ready or available for its intended mission
or for operation. You must do the procedure at the time
stated in the interval column.
(5)
Not Fully Mission Capable If. Column.
Information in this column tells you what faults will keep
your equipment from being able to perform its primary
mission. If you make check and service procedures that
show faults listed in this column, do not operate the
equipment. Follow standard operating procedures for
maintaining the equipment or reporting equipment
failure.
d.
Other Table Entries. Be sure to observe all
special information and notes that appear in you table.
3-4.
Leakage Definitions
The following are definitions of the types/classes of
leakage you need to know to be able to determine the
status of your equipment.
CLASSIFICATION
DEFINITION
Class I
Seepage of fluid (as indicated by
wetness or discoloration) not
great enough to form drops.
Class II
Leakage of fluid great enough to
form drops but not enough to
cause drops to drip from the
item being inspected.
Class III
Leakage of fluid great enough to
cause drops to drip from the
item being inspected.
NOTE
Fluid levels of items with Class I and
Class II leaks must be checked often so
proper levels can be kept.
Class III leaks must be reported to
supervisors or to Organizational Level
Maintenance for corrective action.
Table 3-1. Operator Preventive Maintenance Checks and Services for Crawler-Mounted Rock Drill
Item
Item to
Not Fully Mission
No.
Interval
Check/ Service
Procedure
Capable If:
Crawler and Carrier
1
Before
Hydraulic Hoses and
Inspect hydraulic hoses and cylinders for
Class III leaks are found.
Cylinders
leaks or damaged condition.
2
Before
Boom Drill Carriage
Inspect all drill motor to boom bolt s. If
loose, report to organizational mainte-
nance.
3
Before
Tramming Motors
a. Remove drain plug and drain off
water. Install drain plug.
b. Check oil level. If level is low, notify
organizational maintenance.
4
Before
Rock Drill Reservoir
Check for proper oil level. If level is
low, notify organizational maintenance.
5
During
Hydraulic Control
Visually inspect hydraulic control valve
Class III leaks are found.
Valves
for leaks.
6
During
Air Motor and
a. Inspect air motor and hydraulic
There are unusual noises, motor is
Hydraulic Pump
pump for proper operation. Listen for
sluggish, or equipment is operating
unusual noises. Check for sluggish
erratically.
Motor or erratic performance.
During
b. Check motor exhaust for atomized
Oil is present in exhaust.
oil.
4
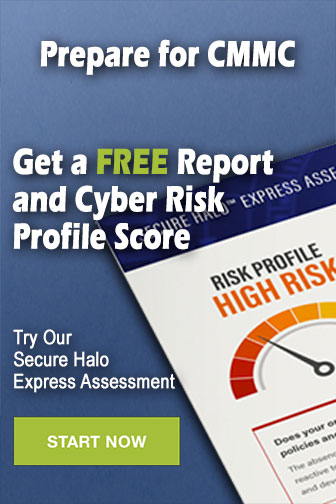