Page 4-9. Chapter 4, Section IV, is superseded as follows:
Section IV. ORGANIZATIONAL PREVENTIVE MAINTENANCE CHECKS AND SERVICES
4-10.
Introduction
a.
General. Table 4-l (PMCS Table) has been
provided so you can keep your equipment in good
operating condition and ready for its primary mission.
b.
Warnings and Cautions. Always observe the
WARNINGS and CAUTIONS appearing in your PMCS
table. Warnings and cautions appear before applicable
procedures. You must observe these WARNINGS and
CAUTIONS to prevent serious injury to yourself and
others or to prevent your equipment from being
damaged.
c.
Explanation of Table Entries.
(1)
Item Number Column. Numbers in this
column are for reference. When completing DA Form
2404
(Equipment
Maintenance
and
Inspection
Worksheet),
include
the
item
number
for
the
check/service indicating a fault. Item numbers also
appear in the order that you must do checks and
services.
(2)
Interval Column. This column tells you
when you must do the procedure in the procedure
column. QUARTERLY procedures must be done every
three months. SEMIANNUALLY procedures must be
done ever, six months.
(3)
Item to be Checked/Serviced Column.
This column provides the item to be checked or serviced.
(4)
Procedure Column. This column gives the
procedures you must do to check or service the item
listed in the Item to be Checked/Serviced column to
know if the equipment is ready or available for its
intended mission or for operation. You must do the
procedure at the time stated in the interval column.
(5)
Not Fully Mission Capable lf Column.
Information in this column tells you what faults will keep
your equipment from being able to perform its primary
mission. If you make check and service procedures that
show faults listed in this column, do not operate the
equipment. Follow standard operating procedures for
maintaining the equipment or reporting equipment
failure.
d.
Other Table Entries. Be sure to observe all
special information and notes that appear in you table.
4-11.
Leakage Definitions
The following are definitions of the types/classes of
leakage you need to know to be able to determine the
status of your equipment.
CLASSIFICATION
DEFINITION
Class I
Seepage of fluid (as indicated by
wetness or discoloration) not
great enough to form drops.
Class II
Leakage of fluid great enough to
form drops but rot enough to
cause drops to drip from the
item being inspected.
Class III
Leakage of fluid great enough to
cause drops to drip from the
item being inspected.
NOTE
Fluid levels of items with Class I and
Class II leaks must be checked often so
proper levels can be kept.
Class III leaks must corrected before
releasing the equipment for operation.
Table 4-1. Organizational Preventive Maintenance Checks and Services for Crawler-mounted Rock Drill
Item
Item to
Not Fully Mission
No.
Interval
Check/ Service
Procedure
Capable If:
NOTE
Checks 1 through 6 are for units
equipped with retrofit kit.
1
Weekly
Feedshell
Check all bolts and nuts on feedshell for
Any bolts loose or
tightness. Pay particular attention to
missing.
drifter drill mounting bolts and feed-
shell slide mounting bolts.
2
Weekly
Feed Chain
Check chain deflection weekly. Ensure
Chain cannot be ad-
that chain is not so tight that no deflec-
justed.
tion occurs not so loose that is sags. Ad-
just if necessary (see paragraph 5-13).
6
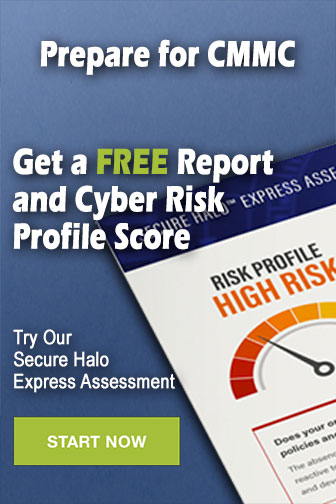