(8)
Carefully check air tube (6) for splits, cracks,
scoring, or excessive wear, particularly in the first 4 in.
where the air tube contacts striker bar. Replace cracked,
split, scored, or worn air tube.
(9)
Inspect plates (39 and 44) for sharp edges and
wear. Remove all sharp edges and hone to clean.
(10) Check inside diameter of front bushing (2). If
inside diameter is greater than 1.285 in., replace front
bushing. If front bushing can no longer be kept tight be-
cause of excessive wear on inside face of front cap (1), re-
place cap.
(11) Check for wear on retainer (26) and both sides
of spring washer (27). Replace if worn.
(12) Inspect gland plug (4) for damage and wear.
Replace if damaged or worn.
(13) Inspect chuck bushing (64) inside carrier (35).
If striking bar imprint is 0.050 in. or greater, replace chuck
bushing (see step (16) below).
(14) Check inside diameter of chuck bushing (64). If
inside diameter is greater than 1.405 in., replace chuck
bushing (see step (16) below).
(15) Check splines on chuck driver (65). If splines
are worn half through, replace chuck driver (see step (16)
below).
(16) To remove chuck bushing (64) or chuck driver
(65):
BLO
A
l
+
H
(a)
Set carrier (35) in hydraulic press as shown.
End A should rest on blocks set far enough apart and deep
enough to allow clearance for the chuck bushing (64) and
driver (65) to be pressed through B. Do not attempt to
press out parts with carrier resting on face C.
(b) Insert fabricated removal tool (see Appen-
dix B) between press and chuck bushing (64) as shown.
(c)
Press chuck driver (65) and bushing (64) out
of carrier (35).
(17) To install chuck bushing (64) and driver (65):
(a) Set carrier (35) in hydraulic press as shown.
Rest face A on blocks.
(b) Using fabricated installation tool (see Ap-
pendix B), press chuck bushing (64), beveled face up, into
carrier (35) until seated.
(c) Using fabricated installation tool, press
chuck driver (65) into carrier (35), using the minor diame-
ter of the spline marks as a guide.
c. Assembly.
(1)
Tap bearing cup (50) into main housing (51).
(2)
Install new gasket (59) and cover (58) on main
housing (51) using four screws (56) and new lockwashers
(57).
(3)
Install new gasket (55) and manifold (54) on
main housing (51) using four screws (52) and new lock-
washers (53).
(4)
Install grease fitting (60) in main housing (51).
(5)
Press two shafts (37) into flange (38). Carefully
orient ends of shafts so that they will properly key into
slots in plate (39) when installed.
(6)
Install gear (45) on each shaft (37).
(7)
Place two bearings (41) and spacer (42) in be-
tween gears (45). Ensure that ends of bearings are slightly
lower than surface of gears.
(8)
Seat motor housing (40) on flange (38). Aline
two dowel pin holes and tap in two dowel pins (36).
(9)
Install air motor gear (43) on flange (38).
(10) Install front plate (44) on dowel pins (36) and
shafts (37) and gently tap in place.
(11) Press three shafts (48) into carrier (35). Install
three nuts (49) and secure with thread-locking compound.
(12) Press bearing cone (46) onto carrier (35).
(13) Slide gear (47) onto each shaft (48).
(14) Set carrier (35) face down and slide air motor
assembly (31) onto carrier. Ensure gears mesh properly.
(15) Press bearing cone (34) onto carrier (35).
9
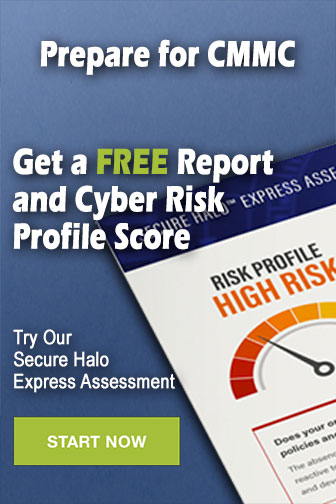